Increase Production by 10% with Uniflow 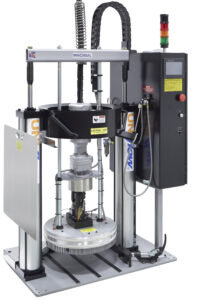
Every hot drum unloader leaves some material at the bottom of the drum, some more than others. That’s frustrating, as nobody likes waste. But to be clear, not every manufacturer is worried about leaving behind a pancake of adhesive.
If that’s so, then why is pumping to the bottom of the barrel important?
How come we’ve been praised (again-and-again) for Uniflow’s ability to reduce adhesive waste by up to 95%? Here’s why.
The Benefits of Pumping 10% More PUR
Manufacturers who use a pressure-sensitive adhesive (or some other product that can be re-melted), don’t much care about lost material waste. All you need to do is remove the remaining material after pumping and place it on top of the next drum, where it gets re-melted. It takes a little time, but there’s no material waste.
If a customer is using a PUR (polyurethane reactive) adhesive that cures with moisture, then any material left behind is totally useless. Sure, they can pull the hardened material out of the barrel, but it’s already crosslinked, permanently, and cannot be melted again.
For these manufacturers, reducing waste is the same as saving money. Every pound of unpumped adhesive they toss is literally throwing away cash. And that’s not all.
With the current PUR Shortages that have resulted from several PUR plants being shut down in Texas, reducing material waste has never been more important. Pumping 10% more material out of every barrel means you’ll be able to increase production at your business with every barrel of PUR.
An additional benefit is the time saved changing out barrels. Pumping all the way to the bottom means you can pump longer, with fewer barrel-changes.
Just How Much Does The Competition Waste?
You won’t believe what the many (many many) comparison tests we’ve run have shown. Competing machines leave a tidy 5-10% of adhesive behind after pumping out a drum. Which may sound good… until you realize how superior a Uniflow machine is.
Uniflow hot melt drum unloaders are amazing.
That’s because we manufacture our platens differently than everyone else, and it shows—after pumping, our machines leave behind just an itty-bitty 0.5%.
Let’s do some math.
PUR adhesive sells for anywhere from $3 to $9/lb. And a 55-gallon drum holds 440 lbs of hot melt at a depth of 30 inches, give or take.
At the end of the barrel—if you’re running one of our competitors’ pumps—you’re stuck with about 1.5 to 3 inches of leftover material, about 20 to 40 lbs of waste.
Do you see how huge this is?
That’s $300+ per drum THROWN AWAY because you didn’t use a Uniflow. What a waste.
Uniflow machines leave about 2 lbs or less; a mere 1/8th of an inch.
We’re proud of that.
WHOA! How Much Does A Uniflow Machine Save?
We mentioned that a Uniflow reduces adhesive waste by up to 95% and that our platens are different. Well, that’s because our platens are machined, not cast.
Our machined platen has 6,000 square inches of heat transfer surface (about double that of any competitor), and the unique fin pattern noticeably reduces the amount of material left in the drum.
Not surprisingly, the more barrels our customers use, the more they save on waste. Here’s a little proof of this in action.
Imagine a company is using 320 barrels of PUR adhesive per year (that’s about 30 per month).
With Uniflow’s ability to pump to the bottom of the drum, they could buy 15 to 30 fewer barrels every year. Now, what if they’re paying $3,000/barrel? How fast do you think it’d be until the Uniflow paid for itself?
We’ll let you think about that before we spill the beans (but here’s a hint—it won’t take long).
- Most of our customers use one drum per day and, often, up to four drums per day. And they have about 220 production days per year.
- A typical drum of PUR adhesives sells for $1,200 to $1,600. Some even up to $4,000/drum.
On the low side, if they get 20 pounds/drum more because they use a Uniflow, that’s a savings of $12,000 annually.
And on the high side, the savings could be greater than $330,000.
Most customers are seeing payback on their Uniflow machine at around 12 months. And we’ve had a few with a 3-month payback—just on material savings.
Is that something you’d like for your business?
Improving Hot Melt Pumping Rates
No matter the hot melt material your company decides to pump, we GUARANTEE that our Uniflow drum unloaders will pump it AT LEAST 40% FASTER. That’s a big claim, and we stand behind it.
For more information on Uniflow® Hot Melt Drum Unloaders or to schedule your free test, call 804-548-4471 or email sales@uniflow.works