Here are a few examples of how spending on the right drum unloader will save your company money.
CUT MATERIAL WASTE BY 10X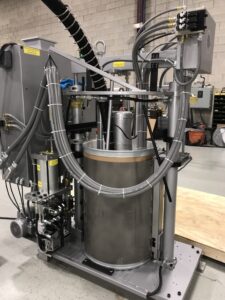
A Uniflow leaves 2 lbs (or less) of material in each drum, whereas all competing machines waste 25 to 40 lbs of material.
That’s a big difference because, right now, PUR costs about $4 per pound. If a quality Uniflow machine reduces your waste by 25 lbs for every drum, that adds up to a savings of $100 per drum.
A manufacturer using PUR at a rate of 200 PPH (pounds per hour) over an 8-hour shift could save $400 per day using a Uniflow. Doing that every day for a year saves $100,000.
As a real-life example, we have a customer using a $12/lb material, running at 400 PPH for 16 hours/day. Using a Uniflow hot melt drum melter saves him $300/drum, $4,800/day, $24,000/week, and $1.2 million/year!
BOOST YOUR PRODUCTION REVENUE
If the speed of your drum unloader is limiting production and sales revenue, switching to the right hot melt drum melter is the solution you’ve been waiting for. A Uniflow pumps at least 40% faster than the competing machines, guaranteed.
Case in point, one of IMMCO’s customers had a rapidly growing product line. Their existing hot melt drum melter could only pump PSA at 400 PPH. It couldn’t keep up with the demand. Upgrading to a low-cost Uniflow Model 4230 enabled them to pump their PSA at 800 PPH, doubling their production volume and revenue.
This is a familiar story. Many of our first-time customers replace a competitor’s machine that isn’t meeting their demands. After getting to know Uniflow they never go back, and some even buy a second or third Uniflow melter as their production ramps up.
Here is a case study showing how a tape manufacturer achieved a 3-month payback by boosting production with a Uniflow.
HOT MELT DRUM MELTER: HIGH-QUALITY UNIFLOW MAKES ALL THE DIFFERENCE
A first-class hot melt drum melter, such as our Uniflow Model 4230, is the best choice for value. Beyond pumping 40% faster than the competition and leaving just 1/8 of an inch of waste in the drum, a Uniflow has many other benefits.
The design options available with Uniflow make your work easier.
- Semi-Automatic Bleed/Boost. This is our most popular option. It lets the operator perform the bleed and boost functions right from the unit’s touchscreen instead of reaching inside a hot drum. Moreover, this feature allows the customer to automatically raise the platen to a park position near the top of the drum to reduce drum-change time.
- RTV-coated platen & drip tray. Hot melt won’t stick to RTV silicone coating, and adhesive drippings can be wiped off in seconds. Going non-stick is game-changing for customers who use PUR.
- Seg-O-Seal® system. Everyone loves our platen seals. They are about half the cost of competitors’ seals, plus they can be installed while the platen is hot. That can save hours of downtime.
IMMCO also offers additional equipment options that add value to your purchase.
A UNIFLOW REQUIRES FAR LESS MAINTENANCE
Our competitors’ units often use piston pumps, which cause parts to wear out and require a constant oil supply for their seal. These pumps are more complex and challenging to maintain than a gear pump.
Uniflow hot melt drum melters make use of a hardened gear pump, which doesn’t wear, requires no oil, and supplies a smooth flow of adhesive to your process.
Many of our competitors also incorporate proprietary circuit boards to control the heat zones in their machines. This solution works, but it means customers are restricted to brand-specific circuit boards with long lead times and inflated pricing.
All Uniflow machines are controlled with PLCs and every component in the electrical panel is off-the-shelf. Many clients have commented on how “open” our design features are, meaning it’s easy to get to everything, and it is easy to diagnose and address issues quickly.
YOU CAN SAVE MONEY WITH A UNIFLOW
At IMMCO, we’ve been building hot melt drum melters since the mid-70s and all of our products are manufactured and assembled in the USA. We’re proud of the reputation that we’ve earned for superior:
- Production rates
- Reliability
- Ease-of-use
- Maintenance
- Worker safety
Click below to see how the Uniflow Model 230 helped one manufacturer, using a high-viscosity adhesive, drastically improve their pump rate.