
PROOF OF CONCEPT / PUMP RATE
FREE TESTING SERVICE
Test drive a UNIFLOW Hot Melt Adhesive Drum Unloader!
Proven results will justify a capital investment. That’s why we offer a complimentary testing service, to demonstrate that a UNIFLOW machine will meet or exceed your requirements before you make any purchase commitment.
We’ll test your material on a UNIFLOW hot melt drum unloader at our facility, and you’re welcome to visit and observe.
UNIFLOW drum unloaders are guaranteed to deliver superior pump rates and reduced material waste, but don’t take our word for it — use our Free Testing Service and see for yourself.
- 1Request a proof of concept / pump rate test
- 2Send us your test material
- 3Observe the testing in person or on video
- 4See the minimal material waste in the drum
- 5Check out our available options
- 6Move forward with confidence in UNIFLOW!
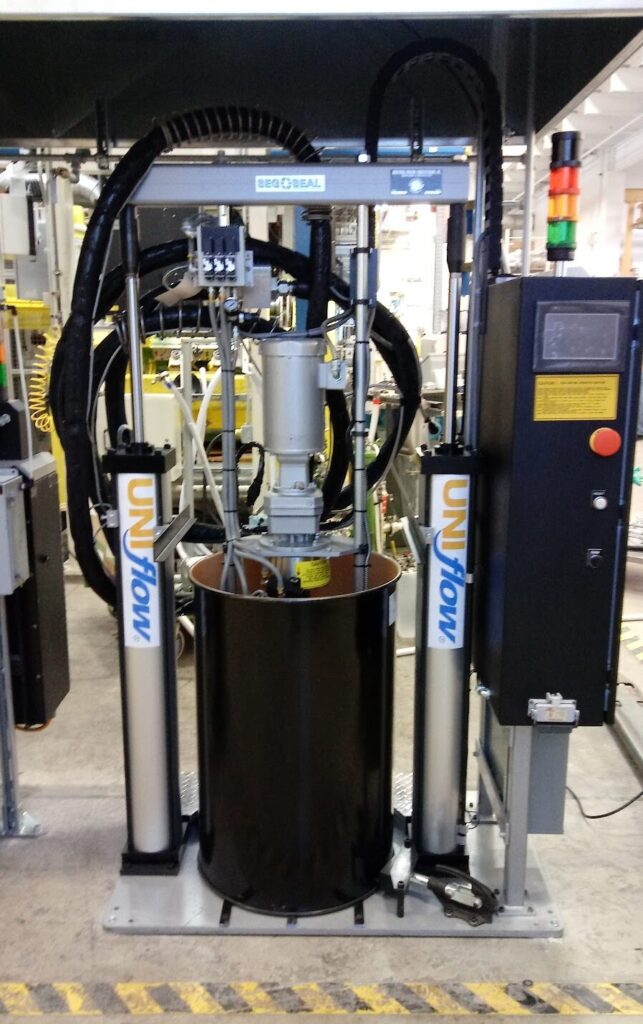
USE THE UNIFLOW FREE TESTING SERVICE
FREE PROOF OF CONCEPT TESTING
UNIFLOW understands the challenge of approving capital expenditures based on expected results. With our free testing service, you can prove that our machines will reach, and in most cases EXCEED, your desired results.
FACTORS AFFECTING HOT MELT DRUM UNLOADER EXPENSE | |
---|---|
Material Packaging | Fiber drums often require clamshell jacketing. Hydraulic clamping can reduce the opening or closing of the clamshell to just 7 seconds. |
Material Viscosity | Highly viscous materials (usually over 100,000cp) may require a hydraulic ram for additional ram force, and/or a high-temperature platen (up to 500°F) for higher application temperature. |
Continuous or Non-continuous Operation | A typical drum change takes 3-5 minutes, but some production operations need to run continuously, with zero interruption. A tandem system for continuous operation will require two drum unloaders, additional heated hoses, and a heated manifold. |
Application / Dispensing Method | Roll coating applications will require a heated manifold; if there is an upper and lower roll coater, an additional manifold and hose will be needed.
Slot die applications may require a high-pressure hose and a heated ball valve. Filtration and/or precision metering will require additional components. |
Ventilation | An exhaust shroud may be advisable to carry offensive or potentially toxic fumes into your existing ventilation system. |
Performance / Reliability | Remote system monitoring can provide for faster troubleshooting, quick repairs, and remote system optimization. |
Speed | Pump rate is increased with higher platen temperatures and higher ram force. The High Pressure Ram option on the Model 4230 will increase the maximum pump rate for many materials, as will the hydraulically-operated Model 230. |
Safety | A semi-automatic bleed/boost function will allow the operator to remain at a safe distance while performing the bleed or boost process. With a manual valve, the operator must work near the heated platen.
An installation with the hydraulic ram option will require heavy-duty clamshell jacketing with hardened c-clamps. |