This case study describes how a Uniflow Model 4230 helped Cascade Windows improve the efficiency of their hot melt butyl application.
HOT MELT DRUM UNLOADER EQUIPMENT MANUFACTURING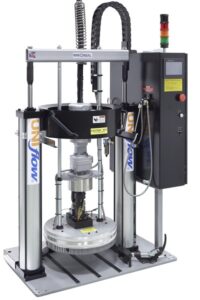
Uniflow drum unloaders pump high viscosity hot melts at higher rates than competing machines – a lot faster. This is achieved with a unique platen that has nearly double the heat transfer area of other platens, leading to higher melt rates.
Benefits realized by using a Uniflow hot melt drum unloader include:
- Dramatically lower material waste
- Faster drum changeovers
- Low maintenance costs
- Safe operation
PUMPING BUTYL HOT MELT OFFERS UNIQUE CHALLENGES
Butyl hot melt is an important component of insulated glass window assemblies. Besides providing excellent adhesion, it has an exceptionally low moisture vapor transmission rate. This is a key factor in producing quality windows that stay sealed for a very long time.
However, Butyl is a thick material that’s very difficult to pump. Even when heated to 190°C (374°F), its viscosity is over 275,000 centipoise. (For comparison, maple syrup at room temperature is around 175 centipoise.) In addition, butyl sometimes has air bubbles in the body of the material in the drum.
HIGHER PERFORMANCE ALL ROUND FROM THE MODEL 4230
Cascade Windows was very familiar with hot melt drum unloaders, as they used both Uniflow and competing drum unloaders throughout their plant. Unlike competing machines, Uniflow drum unloaders did not have to be stopped and purged when they encountered an air bubble. Uniflow left 90 – 95% less hot melt at the bottom of the drum, thereby saving them thousands of dollars. Also, they liked the reliability of Uniflow and the support provided by IMMCO. For all of these reasons, when they needed a new machine they came to us.
We explained that our new model 4230 hot melt unloader was a fraction of the cost of their existing Model 230 Uniflows, but it could still pump hot melt butyl at 300 PPH (pounds per hour.) In addition, the Model 4230 could pump through any bubbles, which avoided the stoppages and downtime.
Lastly, like their existing Uniflow machines, the Model 4230 could almost empty the drum. In comparison, competing machines left 25 – 40 pounds at the bottom.
Cascade Windows was also able to enjoy some of the standard features we developed for the insulated glass industry, as well as options that are available on all new Uniflow machines. These included:
- A proprietary heated hose that resists fatigue and lasts longer than competing products
- A handgun machined from a solid block of aluminum for increased strength and reliability
- A semi-automatic bleed/boost function controlled from the touchscreen for faster and safer drum changeover
THE PURCHASING PROCESS
Cascade Windows placed the order for their model 4230 unloader at the end of August 2019. It shipped to the Cascade plant in Spokane Valley, WA four weeks later and went into service at the beginning of October.
THE RESULTS
With their previous experience of Uniflow machines, Cascade Windows was confident they’d see a host of benefits. Once they put their Model 4230 into production they found it was giving them:
- Higher reliability and less downtime, due to features like the proprietary heated hose and the robust handgun
- Safer operation as the bleed/boost function saved the operator from reaching into the hot drum
- Faster changeovers with the bleed/boost function automatically boosting the platen to a park position after emptying a drum
- No time lost for purging the system of bubbles
- Reduced material costs thanks to being able to empty each drum
HERE’S WHAT CASCADE WINDOWS HAD TO SAY ABOUT THEIR MODEL 4230 DRUM UNLOADER
“We installed a new Uniflow Model 4230 Hot Melt Drum Unloader for our insulated glass line, and we love it. The flow rate exceeded our expectations. We chose to buy a Uniflow because we have used drum unloaders from several other manufacturers, but our 25-year-old Uniflow performed as well or better than the others, with lower overall maintenance costs. Our material waste is low too. The Uniflow leaves only a few pounds of butyl in the bottom, if any. Also, if there is any air in the material, the Uniflow will continue to pump the butyl, although admittedly at a slower volume, until the air is eliminated. Other drum unloaders, in our experience, must stop and have the air bled before they will become usable again.”
– C. Eddie Jones, Maintenance Supervisor, Cascade Windows
SUMMARY & FINDINGS
Butyl hot melt is hard to pump from a drum owing to its high viscosity. The Uniflow Model 4230 hot melt drum unloader was able to pump at 300 PPH, which was significantly more than what competing machines could achieve. In addition, there are far fewer stoppages and less downtime with the Uniflow machine. This results from:
- Ability to pump through air bubbles rather than having to stop for purging
- Faster changeovers with the optional bleed/boost function
- More reliable hose and handgun construction
An additional benefit was a significant improvement in material utilization as a consequence of Uniflow’s ability to almost completely empty each drum.
The bottom line is that the operators, mechanics, and management at Cascade Windows were very pleased with the performance of their Uniflow.
Uniflow equipment can help improve your material utilization, achieving a higher pump rate than competing machines. Find out more by clicking below.